智创未来·西门子工业软件强劲动能赋能高效智造新时代
苹果软件
来源:网络 作者: 编辑:1942920
2025-03-22 12:00:03
浏览:3
评论:0
一、工业软件真能打破制造业的“数据孤岛”?
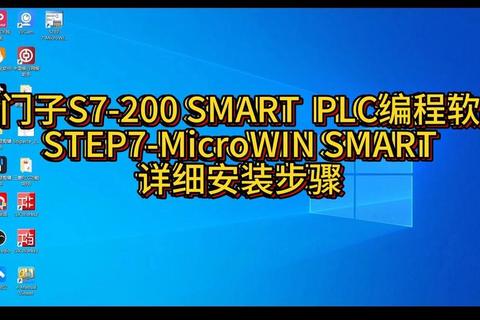
当前制造业面临一个尴尬局面:生产设备、供应链、设计部门的数据各自为政,形成“数据孤岛”。据IDC统计,全球制造业因数据不互通导致的效率损失高达每年1.8万亿美元。而西门子工业软件通过数字主线(Digital Thread)技术,将研发、生产、运维全流程数据串联,让“数据孤岛”变为“智能协同”。
以西门子成都创新中心为例,该中心利用Teamcenter平台实现产品全生命周期管理。某汽车企业通过该平台,将设计变更响应时间从3天缩短至30分钟,并在新能源车型开发中减少40%的物理样机测试。更直观的是西门子能源的案例:通过AWS IoT构建的工业物联网平台,其全球18家工厂的能源数据实时互通,设备维护成本降低25%,机器可用性提升15%。
二、虚拟调试能否让“试错”成为过去式?
传统制造业的试错成本惊人。某机械企业曾因生产线设计缺陷导致3000万元设备报废。而西门子的虚拟调试技术,通过数字孪生(Digital Twin)在虚拟环境中模拟真实生产,让问题暴露在投产前。
东莞蜘网科技为某电子企业打造的智能生产线,使用Tecnomatix Process Simulate进行虚拟调试,提前发现机械干涉风险7处,避免超500万元损失,调试周期缩短60%。西门子与一汽大众的合作更印证了这一技术的价值:通过TIA(全集成自动化)+MCD(机电一体化设计)的软硬件协同仿真,新车产线调试时间从6个月压缩至3周。
三、个性化生产注定与效率背道而驰?
“既要大规模生产,又要满足个性化”曾是制造业的“不可能三角”。但西门子的Opcenter Execution系统,在宁波某服装厂实现每日处理2000个SKU的柔性生产。该系统通过智能排产算法,将设备利用率从68%提升至89%,订单交付准时率提高35%。
更颠覆性的案例来自西门子与蓝箭航天的合作。在卫星发动机精密部件制造中,NX软件的创成式设计功能,结合3D打印技术,将单个零件设计时间从2周降至8小时,材料消耗减少45%。这种“批量定制”模式,正在重塑高端装备制造业的游戏规则。
智创未来·西门子工业软件强劲动能赋能高效智造新时代的实践表明,制造业的进化方向已清晰可见。对于企业而言,可采取三步策略:
1. 优先引入数字孪生技术,将关键产线的虚拟调试纳入标准流程(参考网页5/6/24的实践路径);
2. 建立跨部门数据中台,打破研发、生产、供应链的数据壁垒(参考网页44/68的架构设计);
3. 选择开放性工业云平台,如MindSphere,避免被单一供应商绑定(网页44/93的转型方案)。
智创未来·西门子工业软件强劲动能赋能高效智造新时代的征程中,企业的核心竞争力不再局限于设备规模,而是取决于数据流动的速度与智能决策的精度。正如西门子成都创新中心展示的数字化双胞胎,虚实融合的生产模式正在重新定义“制造”的边界。智创未来·西门子工业软件强劲动能赋能高效智造新时代,既是技术革命,更是一场关于制造思维的重构。
相关文章:
文章已关闭评论!