高效无缝离线编程软件智能驱动智能制造极速升级
热门软件
来源:网络 作者: 编辑:1942920
2025-03-19 21:30:02
浏览:4
评论:0
智能制造时代,离线编程是“效率神话”还是“纸上谈兵”?
当工业机器人以每年超30%的增速渗透到汽车、3C、新能源等产业时,一个矛盾愈发突出:一边是产线对柔性化、高精度生产的迫切需求,另一边却是传统示教编程效率低下、停机调试成本高昂的困局。据统计,传统工业机器人编程调试耗时占项目总周期的40%以上,而复杂装配场景中因路径规划失误导致的返工率高达15%。在这个背景下,“高效无缝离线编程软件智能驱动智能制造极速升级”成为行业热议的焦点——它究竟是突破效率瓶颈的利器,还是脱离实际的理想化工具?
一、效率瓶颈如何被“虚拟仿真”击穿?
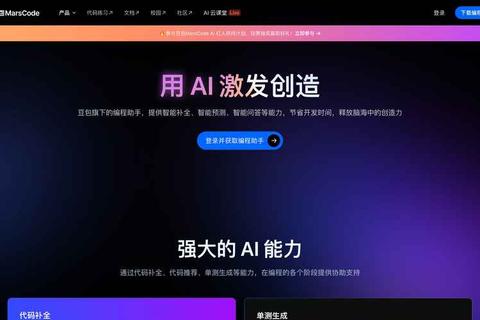
传统编程模式下,工程师需在现场逐点调试机器人的运动轨迹,不仅耗时费力,更可能因人为误差导致碰撞风险。而高效无缝离线编程软件通过三维建模与虚拟仿真技术,将调试环节从车间转移到计算机,实现“零物理接触式编程”。
以徐工集团为例,其起重机械部门引入FASTSUITE飞思德软件后,焊接触碰寻位算法适配效率提升200%,新物料到厂前程序已准备就绪,编程效率翻倍。这种“先仿真、后执行”的模式,让机器人在虚拟环境中完成路径优化与碰撞检测,仅需将验证后的程序一键下发至实体设备,停机时间从数周压缩至数小时。数据显示,采用此类软件的企业平均减少调试成本35%,项目交付周期缩短50%。
二、复杂场景如何靠“智能算法”精准适配?
在电机装配、雷达天线组装等精密场景中,毫米级的路径偏差就可能导致产品报废。传统示教编程依赖工程师经验,而高效无缝离线编程软件通过智能算法,将CAD模型中的装配约束关系转化为机器人运动轨迹。
越擎科技的iRobotCAM软件正是典型案例。其基于三维CAD平台开发的装配工艺规划系统,可自动提取零件间几何约束,生成无碰撞运动路径。某3C电子企业应用后,机器人装配精度从±1.2mm提升至±0.05mm,工艺规划耗时从3天降至4小时。这种“数据驱动决策”的模式,结合深度学习算法对历史工艺数据的分析,还能自主优化轨迹平滑度与节拍时间,让复杂装配的良品率提升18%。
三、多品牌设备如何实现“跨平台协同”?
制造业企业常面临多品牌机器人共存的现实难题。传统解决方案需针对不同品牌编写独立程序,而高效无缝离线编程软件通过开放式架构,打破设备间的技术壁垒。
FASTSUITE飞思德为徐工定制的解决方案,成功集成库卡、发那科等6个品牌焊接机器人。软件内置的通用后处理器可将仿真程序自动转化为各品牌控制器识别的代码,并生成标准化焊接报告。类似地,RoboDK平台支持500余种机器人模型,用户只需拖拽式操作即可完成ABB、安川等设备的协同路径规划。这种“一次编程,多端执行”的能力,使某汽车零部件厂商的设备利用率从65%提升至89%。
向“数字孪生”要生产力:企业转型三大行动指南
要让高效无缝离线编程软件智能驱动智能制造极速升级真正落地,企业需分三步走:
1. 选型适配:优先选择支持主流CAD格式(如SolidWorks、CATIA)且兼容多品牌机器人的平台,例如iRobotCAM或FASTSUITE,避免数据转换损失;
2. 数据筑基:建立高精度三维模型库与工艺参数数据库,定期校准机器人运动学参数,将定位误差控制在±0.1mm以内;
3. 人才升级:培养既懂机械设计又通晓Python脚本开发的复合型工程师,利用AI辅助编程工具提升人机协作效率。
正如广汽新能源焊装车间通过数字孪生技术将调试周期缩短35%的实践所示,离线编程已从“可选项”变为“必选项”。当虚拟世界与物理产线深度交融,制造业的智能革命才真正步入快车道。
相关文章:
文章已关闭评论!